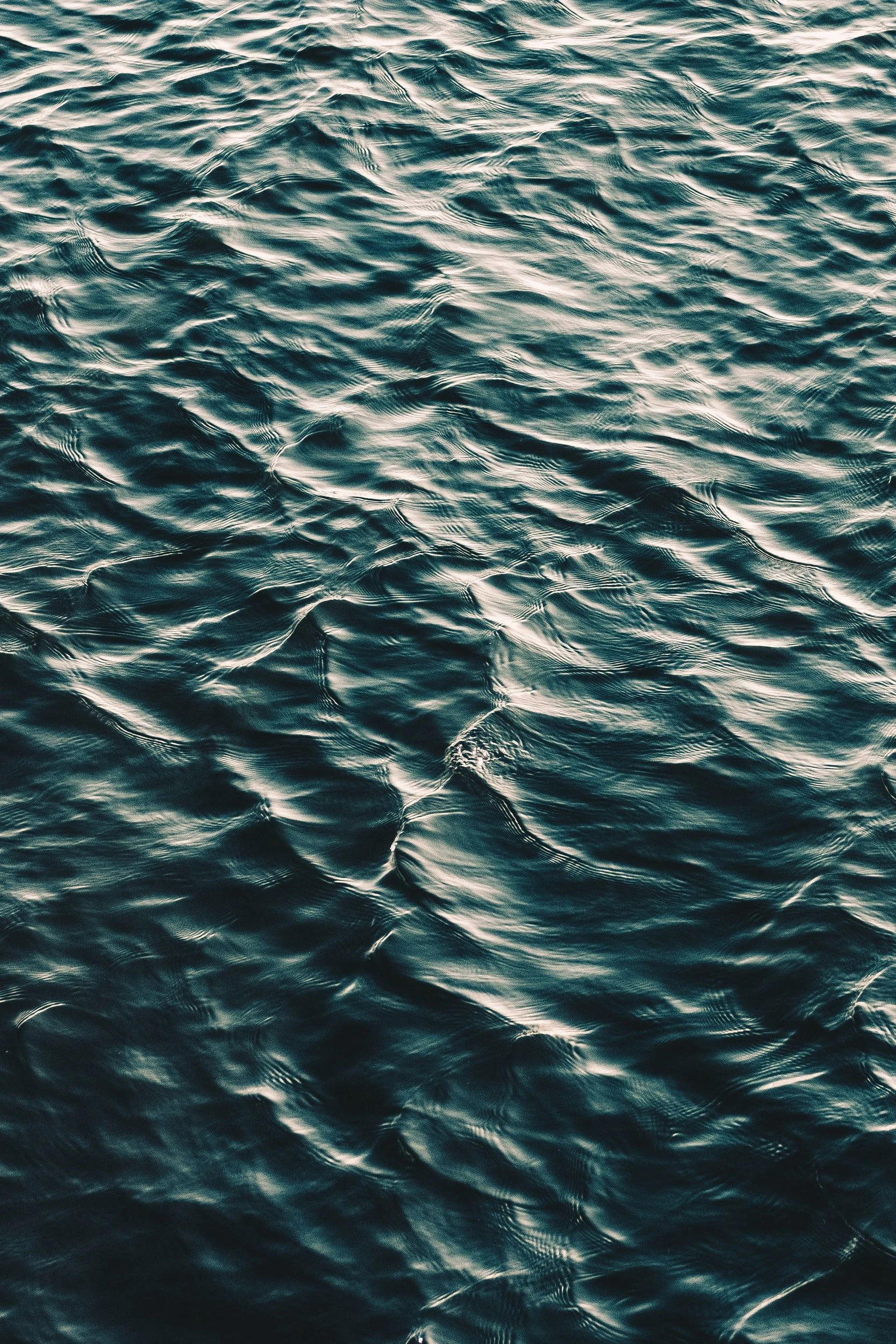
Inspections are a crucial part of facility maintenance. Inspections can help prioritize maintenance, assess safety issues, establish a baseline condition before change of ownership and extend the service life of a facility.
Types of Inspections
-
Routine Inspections
Routine inspections are regularly scheduled inspections based on the condition of the structure. These inspections are designed to allow marina owners to be proactive with maintenance of the facility.
During a routine inspection, damage ratings are determined for each of the components within the defined scope of the structure. The ratings provide a baseline for future inspections.
The maximum intervals between routine inspections, as recommended by the American Society of Civil Engineers (ASCE), can be found below.
-
Post-Event Inspection
Post-event inspections should be conducted after major storms, boat collisions or any other event that can cause damage to a structure.
These inspections quickly evaluate a structure to evaluate potential damage and determine necessary repairs. Depending on the type of damage that occurred, it may be necessary to remove marine growth to accurately.
Storms can bring in a significant amount of debris. It is recommended that any post-storm inspection include a full bottom survey.
-
Construction Inspections
Construction inspections are used as quality control for new construction, repairs, or upgrades.
These inspections can also be used to provide detailed information needed to make engineering decisions prior to making upgrades or repairs.
Bottom surveys are recommended prior to the commencement of all new construction projects. A visual and tactile inspection of the seafloor can be used to map bottom type and controlling depths. It can also identify debris that could potentially hinder construction.
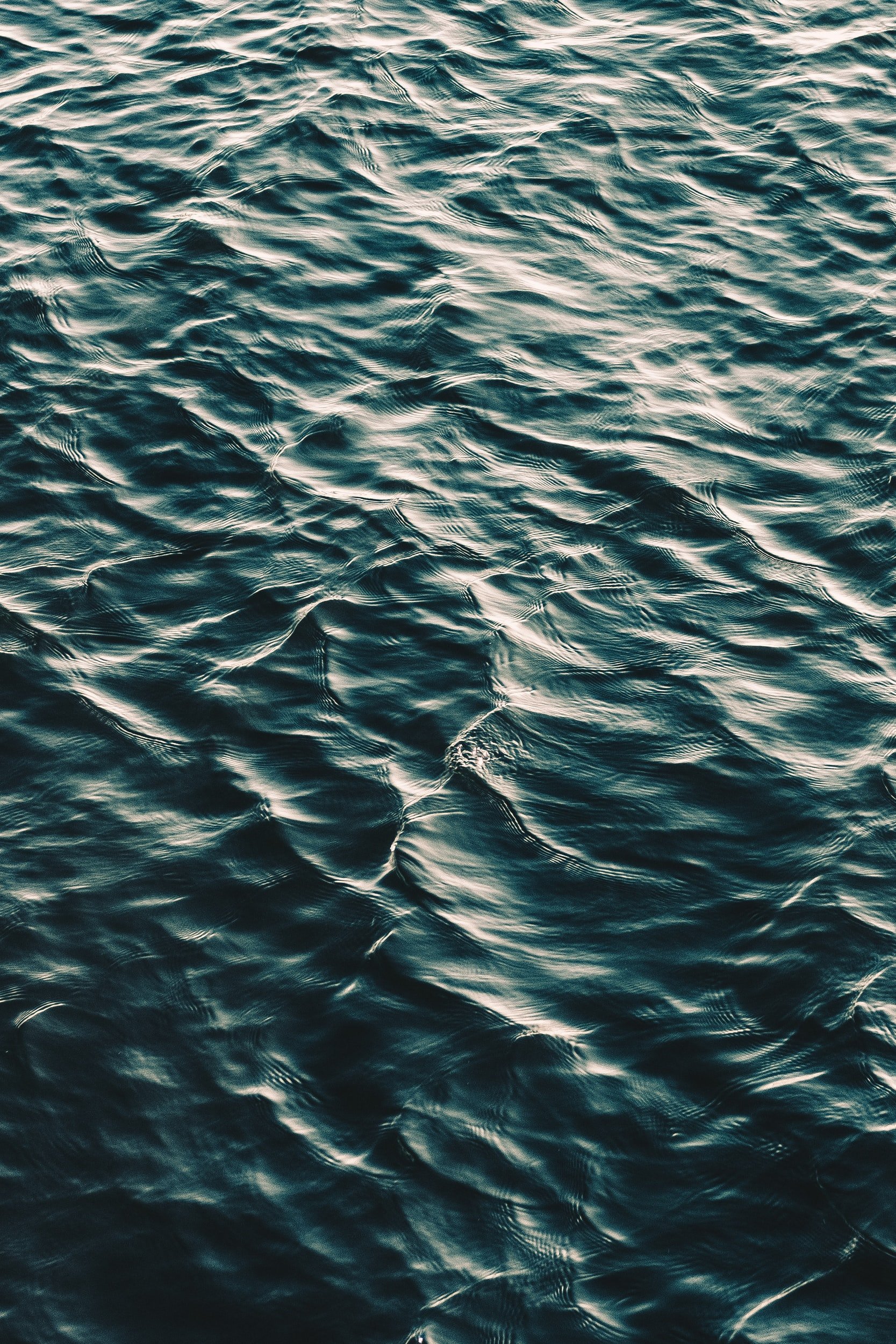
Recommended Routine
Inspection Intervals
-
Unprotected Timber or Steel Structures
Maximum inspection intervals for unwrapped timber and steel without protective coating or cathodic protection are as follows:
Saltwater, brackish water or freshwater with current over 0.75 knots
Good or Satisfactory Condition 4 years
Fair or Poor Condition 3 years
Serious Condition 1 years
Critical Condition Every 6 monthsFreshwater with less than 0.75 knot current
Good or Satisfactory Condition 6 years
Fair Condition 5 years
Poor Condition 4 years
Serious Condition 2 years
Critical Condition 6 months -
Concrete, Composite Material, Protected Timber or Protected Steel
Maximum inspection intervals for wrapped timber, concrete, composite materials and steel with protective coating or cathodic protection are as follows:
Saltwater, brackish water or freshwater with current over 0.75 knots
Good or Satisfactory Condition 5 years
Fair or Poor Condition 4 years
Serious Condition 2 years
Critical Condition 6 monthsFreshwater with less than 0.75 knot current
Good or Satisfactory Condition 6 years
Fair or Poor Condition 5 years
Serious Condition 2 years
Critical Condition 6 months -
Bottom Surveys/Debris Removal
Maximum inspection intervals for bottom/mudline surveys are as follows:
Saltwater, brackish water or freshwater with current over 0.75 knots
Bottom surveys should be conducted every 2 years or after major storms.
Freshwater with less than 0.75 knot current
Bottom surveys should be conducted every 6 years or after major storms.